by Doc Justice
“ A kit with two lavs and a boom is standard. ”
“ It’s standard to record to two different media sources. ”
“ A mono scratch track to camera is standard practice. ”
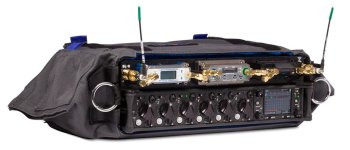
Just who sets these standards anyway?
For professional sound mixers, social media has become an indispensable tool for networking, for learning about new equipment, new techniques and for job advice. Lately, it has also become a place forum to develop unwritten rules within our own community.
We all benefit from learning the do’s and don’ts of work ethics from each other. Unfortunately, the “workflow standards” that get tossed around online do little more than to divide us in choosing sides of an argument. Posting about these types of “standards” often results in belittling those that don’t live up to them.
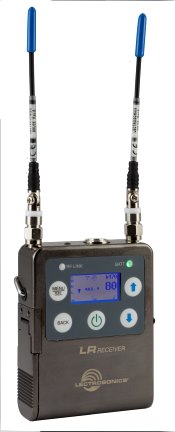
Even the manufacturers that design the equipment have their own guidelines on “standards.” “From a manufacturing point of view, when we say standards, what we’re looking at, is something that has been established by a committee,” says Gordon Moore, President of Lectrosonics. “What we’re talking about here are common practices.”
The distinction between standards and common practices is important, particularly for product development. “Common practices have every effect on the products we create,” continues Moore. “We have different receivers available. When we are looking at movie and location guys, how they use it in a bag or on a cart; that affects the design. For example, when we designed the LR receiver, that was designed for the DSLR. “It’s a challenge to try to design a product to appeal to as many people as possible. If you make a product too broad, then you fail to serve anyone and you end up with a product that doesn’t fit anywhere. When we designed the LR, we really did have specifically the DSLR miniature requirement in mind. That’s what drove it. We couldn’t put an LCD on top of the unit since other things had to go there. That goes against a bag setup, but we have bag units. You make it specific to a task, and let people adapt. Don’t compromise it too much. It’s a juggling act, it really is.”
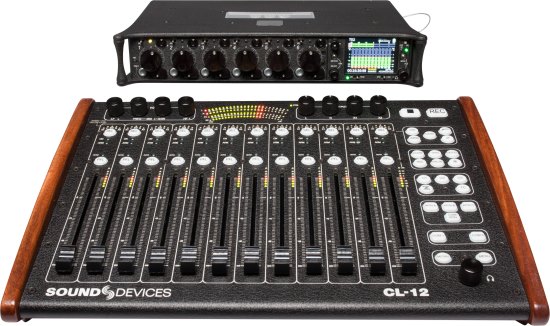
Sound Devices President Paul Isaacs has other thoughts on product development. “Personally, it’s not about creating standards for the sake of standards. A standard is created to serve a purpose. What Sound Devices is always striving for is to always make our customers’ lives easier, to make the workflows smoother, more efficient, and to make them more effective as sound mixers and cinematographers. It’s not so much the standard that guides things; the standard is a result of our desire to improve the working lives of our clients. SuperSlot comes from that desire.”
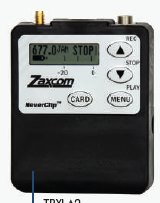
SuperSlot is a new standard developed by Sound Devices, with input from several other manufacturers. “SuperSlot evolved from a mounting standard that existed earlier, called UniSlot, a 25-pin, defined connector that Panasonic and Ikegami came up with so you could mount receivers on a camera and send audio wirelessly. UniSlot was developed to make it easier with one simple connector. We wanted to use something similar for the mixer/recorder in the bag, so that we could eliminate cables and the amount of cable spaghetti in bag.
“If the wireless manufacturers weren’t on board with it, there was no point in going down that path. We got in contact with Sennheiser, Lectrosonics, Wisycom and Audio Limited to get their thoughts. We worked with them so that everybody was happy.
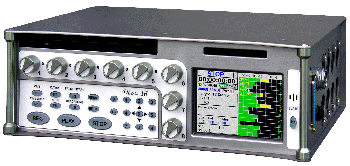
“We’re all for standards at Sound Devices. We’re not at all for proprietary protocols, but open standards. We very much want to open up design options so that any manufacturer can work with our products, like the 6-Series recorders.”
Zaxcom is another manufacturer that has helped to develop standards. CEO Glenn Sanders says, “Zaxcom invented prerecord, which was born out of using buffered data, and now everybody else uses it. We invented the process of using Sceen, Take and Note meta recorded on a audio file with production sound. Zaxcom worked with Avid to make the metadata directly readable on Avid and Pro Tools systems.
“I hate the term ‘closed-system,’” continues Sanders. “I think we are anything but a closed system. Zaxcom has a unique system, due to the fact that there is nothing on the market for it to be compatible with. We feel strongly about Zaxnet’s benefits.”
It is no surprise that the manufacturers who make sound equipment have different philosophies in product development. Competition between them helps drive innovation, yet satisfying the needs and wants of their customers remains the most important motivation.
Moore of Lectrosonics says, “We do a lot of market research, people don’t realize how much we talk to the guys in the field. When we are introducing a product, IATSE members are our core customers. We know them well and have personal relationships with them. We’ll go to an event and invite people to bring their thoughts. You can’t believe how many meetings we hold internally before green-lighting a new product. When we bring out a new product, it’s because we talked to a lot of people. We’re looking for the BEST of everything, but you can’t include everybody’s idea of what’s best.
“That’s why you get different products that do different things. That’s why we have so many variants on transmitters. All of these are variations on a theme trying to meet the different needs of the market.
“We look at common practice of using a Lemo connector in certain environments. The theater environment uses the Lemo connector a lot. For our transmitters, we picked the Switchcraft 5-pin product based on durability. We found that the TA5-Series connector was more robust and survived destruction testing opposed to the Lemo.
“This was done way back in 1987. We standardized our design based on that because, in our book, it was a more reliable, tougher connector.
“When we got to the SSM, we looked elsewhere. The defining factor was size. It had to be full-featured, it had to be as small as possible, it had to run for four to five hours. We got it up to six. The driving criteria were size, size, size. The Lemo made sense because that was the other most common connector.”
Moore and Lectrosonics were able to identify some of the common practices of their customers, and make sure to cater to their needs. Paul Isaacs of Sound Devices presents a similar take on this theme.
“We are totally guided by our customers’ needs. Occasionally, we’ll throw things out there they didn’t know they needed.
“ I’m looking to redefine workflow. There’s innovation and there’s change. I want to show people that there is something better. ”
–Glenn Sanders, Zaxcom
Dante is an example of that. When we got into Dante, nobody was talking about it at all. When we released it, it quickly took hold and now there’s no looking back.
“It’s a two-way conversation. We push things out there, and users feed back what they want. It’s a handshake process. But if we need to adhere to a particular standard so our customers have a simpler life, we will support that.
“In terms of drive formats and file formats. The recording needs to fall in line with post production. We’re very aware if it doesn’t easily fall into place, productions will just reject that equipment. The cost of doing workarounds in post production to make nonstandard formats fit in is huge. Production companies are guided by budgets that are always being cut, so if you do something in a nonstandard way, those companies will say ‘nope, it’s not going to happen.’
“We’re constantly thinking of ways to improve the workflow. We put in MP3 capability since some users need transcription files. We’re always looking to fit in with common practices.
“We want to make sure we support the widest consensus we can. NP-1s have been widely used for many years so designing around that battery was key. Even though it’s not the ‘best’ battery available these days (there are alternatives available), it is the most popular. Even considering antenna connectors, we went with the BNC connector since that was what the users wanted.
“Should there be a feature that needs to have a standard and there isn’t one in existence, we’ll create it. We won’t keep it to ourselves. We’ll share it, and SuperSlot is a fine example of that.”
Glenn Sanders’ view is a bit different. “I’m not scared of taking risks. Damn the torpedoes, full speed ahead. You gotta take risks. If you don’t, you end up making the same stuff that everybody else makes and that’s not exciting. I want to make cool stuff. I want the people who are willing to go out with features and abilities and use them to impress people. That’s what we do. Life is boring without that. I’ve never been accused of being boring.
“User’s workflow is the most important thing. We have to understand what the customer is doing with the product. What the expectations are from getting it as a new product, installing it on the cart, what it’s going to interface with, what the media will be, how post production will deal with that media.
“You buy the gear, and based on what the gear can do, then you know what your workflow is. You could buy Zaxcom gear and have different workflow than somebody else’s gear. Your workflow might be with Zaxcom recording on the transmitters and only recording on transmitters. That could change the whole production! You can’t do that with anything else.
“I’m looking to redefine workflow. There’s innovation and there’s change. I want to show people that there is something better.”
These are the views of just three of the more popular manufacturers in our industry, and there are dozens and dozens of others. Each of these companies shape their products based on their own unique views of how to best satisfy their customers’ needs, which are also constantly shifting.
As Sound Mixers, we make purchasing decisions for many different reasons. Some choose to pursue aggressive upgrade paths to keep up with the most advanced feature sets. Others only buy out of necessity; when their current gear becomes obsolete. Some purchase with an eye toward the future, while others treasure backward-compatibility.
Our profession is not black and white. There is no line between right and wrong decisions. There are no written standards for how to mix, which equipment to buy and how to run a business. There are no requirements for manufacturers to include or exclude features other than to follow their own beliefs on how to serve their customer base. There is no set standard.
When purchasing, make decisions that suit you and your work best. The only standard that matters is the one you hold yourself to.