by Devendra Cleary CAS
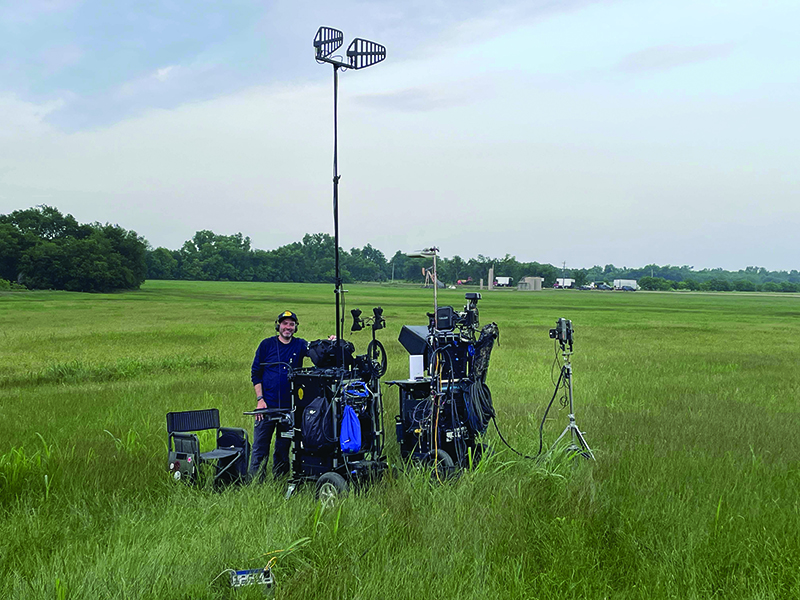
CHASING THE MOVIE
In late 2022, I had the distinct pleasure of meeting and working with the very talented director Lee Isaac Chung. We met on the first day of filming his episode of Star Wars: Skeleton Crew. And as much as I’m excited to write about Star Wars, this article is about chasing tornadoes! Isaac had told me after the Christmas 2022 holiday break that he was asked to direct Twisters for Universal Pictures and was hoping to get me on his team. It was early in the process, but hopes were high. My name was certainly in the hat and I had several instances of correspondence with the production team. It was just a waiting game. There were many decisions yet to be made on the studio level as to where filming would take place before settling on the decision to shoot the entire thing in Oklahoma where the story is set. Then, on an afternoon in mid-February 2023, I got the call from the UPM offering me the movie! I was shocked and ecstatic and at a loss for words. Filming was set for early May 2023 and we’d be in Oklahoma the whole hot summer.
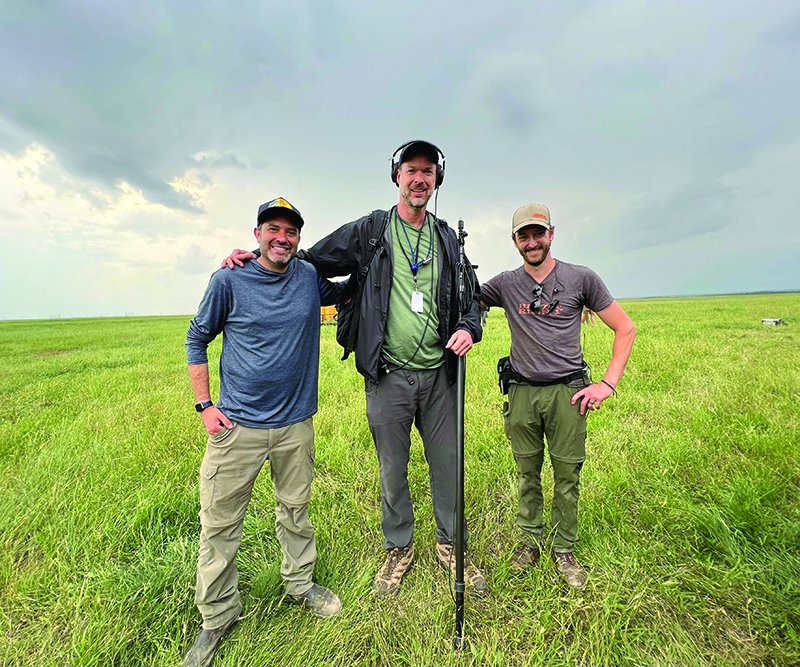
CHASING MY CREW
I have time-stamped proof in my phone that the absolute first thing on my Twisters checklist was to hire Patrick Martens to be the Boom Operator. This is a supervisory position and a highly skilled, technical, and artistic job that requires people skills and both an immense amount of knowledge and experience with sound. I’ve known Patrick since the first day filming second unit of Angels & Demons in 2008 where I was his Utility Sound Technician. His express set of skills, experience, and charm (plus the fact that I consider him a very close friend) made him a shoe-in to fill this extremely important position that I could not do the job without. Luckily, Patrick was a go for Twisters!
Next on deck was to navigate the process of hiring a local Oklahoma Utility Sound Technician. I didn’t know anyone in this particular market, so I had to start from scratch. Production provided a list of local union and nonunion sound professionals and there is a community of expats and crew residing in the area that are covered by the Area Standards Agreement. I interviewed six candidates before landing on Brian Gililland. Born in California on an Air Force base, Brian traveled around as a military brat before he finally settled in Oklahoma City. He’s a member of IATSE Local 484 in good standing, a phenomenal human being, delightful to be around, enthusiastic about the craft, and way more experienced than I realized when I picked him. Basically, we hit the jackpot and I felt very lucky to have him on board.
CHASING A PROCESS
Most of us in production sound have done a fair share of moving-vehicle work. The big differences on this production were the sheer amount of it, the fact that we intended to do it practically, and the overwhelming variety of principal picture cars that were intended to interact in both a stunt and dialog capacity simultaneously. This is a tornado-chasing movie after all, so working at a fast pace while block shooting multiple versions of the same characters’ picture cars with very high expectations from a director whom I adore and producers whom I had yet to win over was on the forefront of my mind. I’ve been trying to find a stronger word than “intimidating.”
During pre-production, I learned that only a very small percentage of the car scenes were going to be done static on stage as “Poor Man’s Process” shots. Only very, very heavy wind, rain, hail, and destructive tornado elements were to be done on stage, overseen by our genius Special Effects Artists and with our VFX Artists filling in the rest. This was a creative decision born out of necessity owing to just how powerful the weather conditions in the storyline were for each of those specific scenes. But the production’s goal was to shoot as much heavy wind, rain, hail, and tornadoes practically and out on the real dirt roads.
My team needed multi-pronged solutions to achieve practical moving-car work with a large cast, a lot of chaos, and a heavy reliance on pod-driven picture cars instead of more typical tow-rig configurations.
What is a pod-driven picture car? Otherwise known as pod cars, they are modified cars used in production. Typically, a driving pod is mounted on top of the vehicle and a series of cables connect the controls with the drive train, steering, and brakes. As I’m sure this voids the car’s warranty, saying it’ll be driven by a stunt driver probably accomplishes the same. These pod-driven vehicles allow for the actors to sit in the car without being burdened with the dangerous task of driving and acting at the same time. It also allows for more complex maneuvers at faster speeds that aren’t always possible on a camera car rig that tows the picture car.
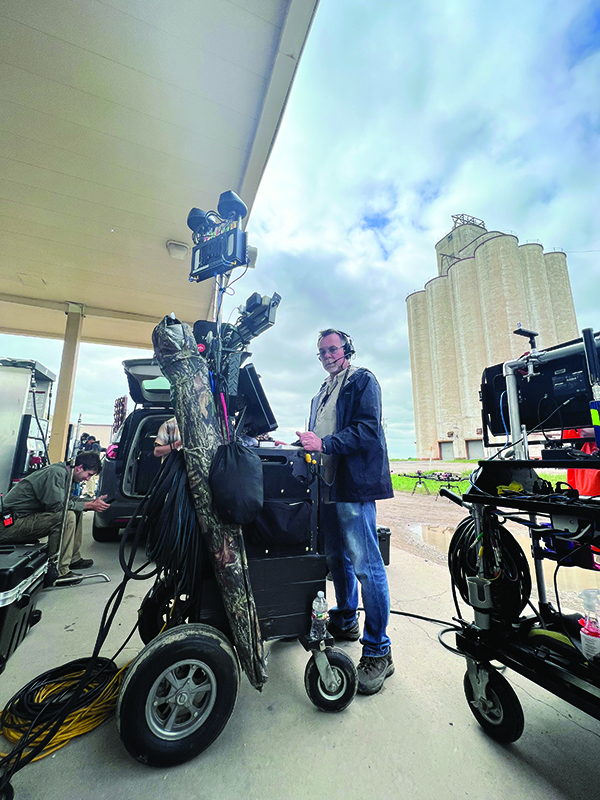
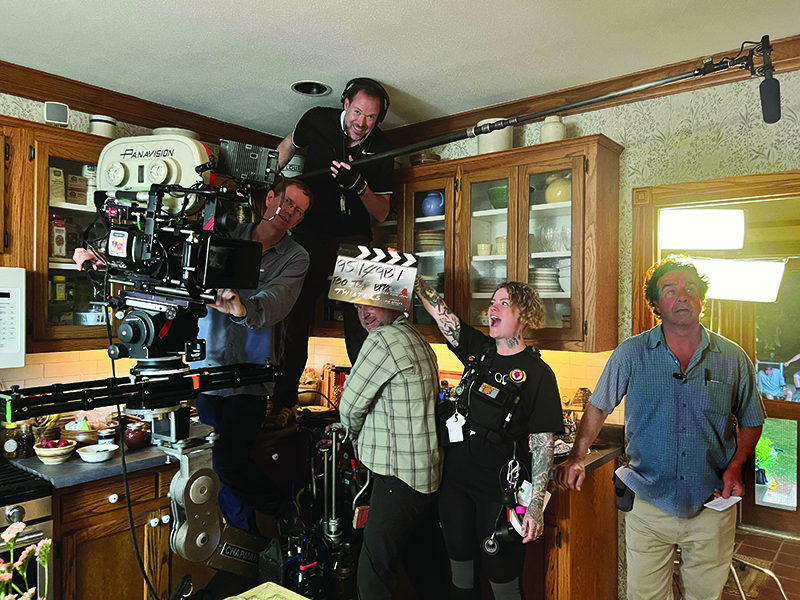
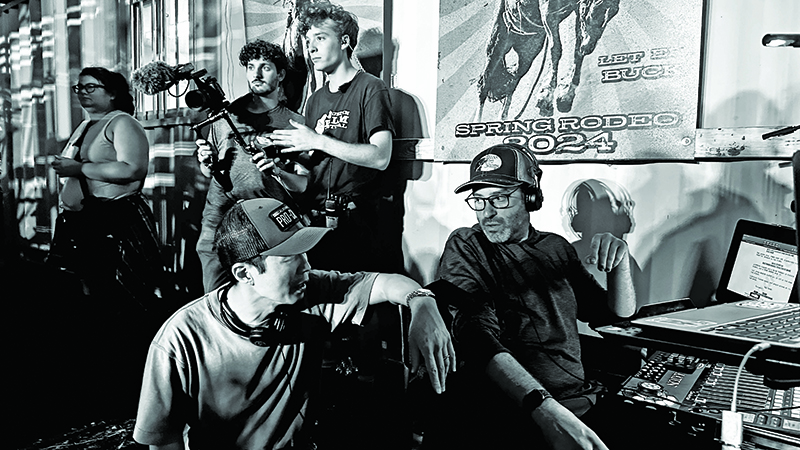
We did still in fact utilize camera car tow rigs. We had a bespoke vehicle called the “MTV Rig,” which was a camera car with a Pro Cam-provided Technocrane mounted on it. This rig would tow the picture car and perform dynamic crane shots of the cast while moving. This rig had the traditional sound mixer spot up front in the passenger shotgun seat. However, with all the camera assistants, lighting programmer, assistant director, crane operators, and special effects technicians; there was not enough room for both Brad Ralston (our Video Assist Operator) and myself, plus all of our gear to conformably operate on this rig. The possibility of finding a spot for me on the rig without being near video assist posed major director monitoring challenges and made it difficult to provide a robust audio feed to Brad for clip review and playback. So, we were constantly stretching the wireless range of our audio equipment to its fullest capacity.
On top of those challenges, the plan, as mentioned earlier, was to have the ability to “block shoot.” This meant we would be set up in one particular character’s picture vehicle that was being towed by the MTV rig and then set up in a double of the same character’s picture vehicle outfitted as the free-driving pod car.
For us, this meant it made way more sense to ride in the follow van alongside video assist. I set myself up with a miniature sound cart in the back end of the follow van. This was nice because I was able to keep everything built, including a PSC EuroLiFe power system, a large video monitor, and my heftier bag rig that consisted of an Aaton Cantar Mini, five Lectrosonics DCR822’s, an antenna distribution unit by Audio Wireless, and two Lectrosonics IFB T4’s; all bound together in a custom-made Protogear bag and a custom-made Sound Guys Solutions shelf bracket. The video monitor allowed me to both interface with my Lectrosonics receivers using Wireless Designer, as well as receive the SDI video feed. Video assist was in the front side of the same follow van, so we provided a hardwired feed to them, with a close range IFB feed to the director and producers who were also in the van with us. This was something of a double-edged sword. We never needed to de-rig from the MTV tow rig and then re-rig right back to the follow van for the pod-driven shot. When we would hurriedly swap over to the pod-driven version of the picture cars, we were only a few plant mic tweaks and bag-drop rig position swap away from being ready to roll. On the other hand, this meant that when we were filming coverage using the MTV rig, we were much further away. Instead of being just twenty-five feet away from the picture car with my receiving log periodic shark fin antennas, I was more like two hundred feet away with the tractor/trailer length, plus the speed space distance from the picture car.
Production would favor the pod coverage often because it was much faster and nimbler. The real treat of the pod-car coverage was it was fairly close to our follow van and without the giant wall of metal that was the MTV rig.
For Patrick and Brian specifically, this meant planting doubles of our plant mic arms, doubles of our mic hangers, doubles of our digital wireless transmitters (when possible), doubles of our XLR patch cables and doubles of our rooftop-mounted transmitter antennas and corresponding transmitter antenna cables. Even though the pod cars were typically very close to us, they would occasionally be used in such a way that allowed for free-driving greater distances from the follow van; but with these special instances, I was glad to have such a fast, flexible, and hardworking crew working with me, as well as some of the extra special tools I will describe below.
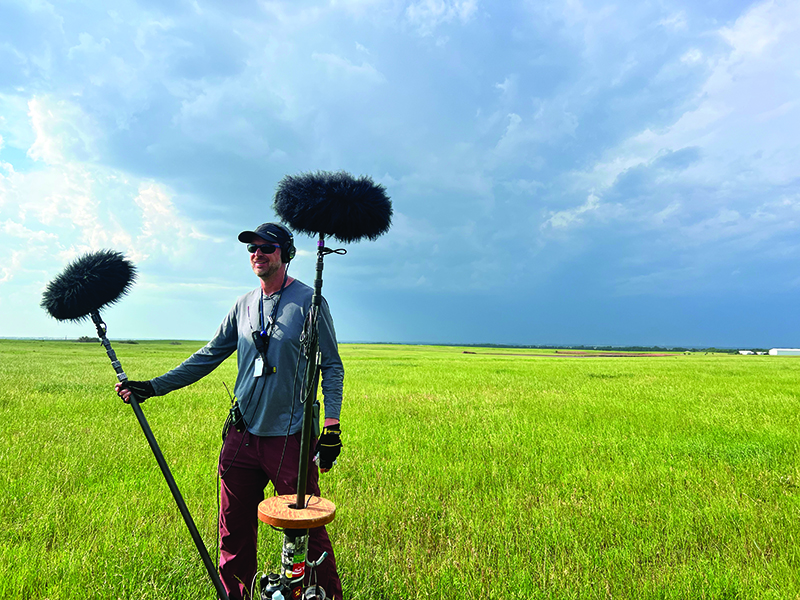
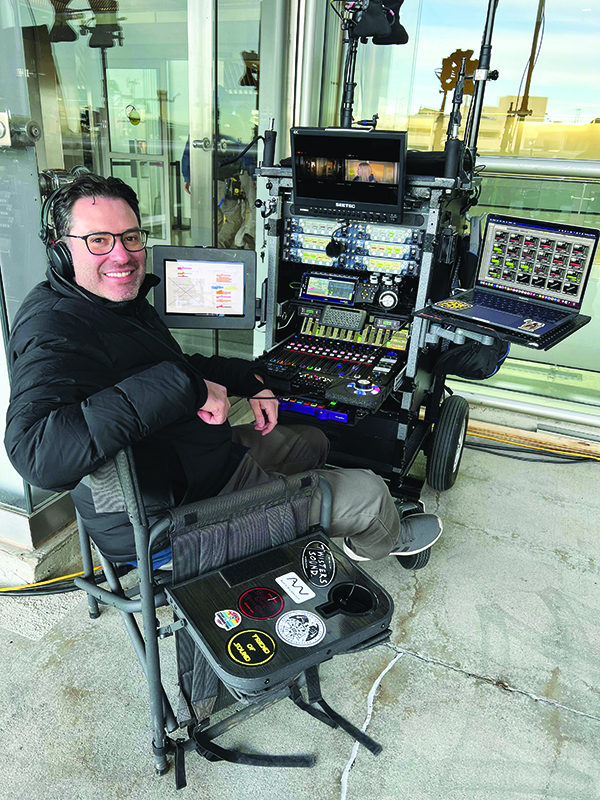
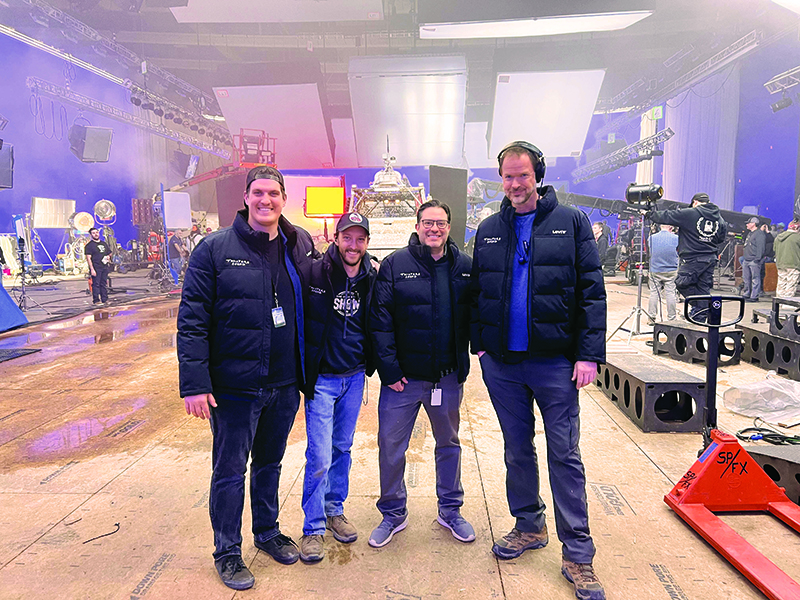
OK, a few things that I think bear some detailed explanation: our plant mics and what we used, our rooftop transmitter antennas (which were to my surprise, the first layer of the “secret sauce” that really made achieving all of this possible), and then my bag-drop rig which performed well above my wildest dreams! So much that it deserves its own section.
But first, the microphones and transmitters. I’m a little bit old school, so I favored the use of my Schoeps CMC6/MK41 mics. The transmitters for these plant mics were all digital Lectrosonics DPR-A plug-on transmitters with phantom power. For the majority of our practical driving work, I really needed the reach and isolation that the Schoeps provided Plus, I really like how they sound. So, I purchased two more Schoeps microphones, but this time I opted for the CMC1 pre-amp body and two more MK41 capsules. There’s no such thing as having too many microphones in your kit. This was super handy for the very common scenario where we had all four seats in a vehicle occupied by a principal cast member. For these scenarios, we would plant all four Schoeps mics. Typically, the CMC6’s in the front and the CMC1’s in the back. We maintained this configuration even in scenes with just two performers because of the tendency for the blocking to include the actors turning around and looking backward. Two plants per actor, no waiting! They were all mounted with swappable length “Ken Strain Arms,” low-profile right angle XLR patch cables, and then 12-foot-long thin wire SMA to SMA antenna cables that ran all the way to the roof of the picture vehicle to the Audio Workbench mag mount antennas. These antennas (shown in the flowchart at the end of this article) use a magnet that is connected to the ground and shield of the coaxial antenna connection and when it is magnet-mounted to the top of the steel rooftop of the vehicle, it uses the entire steel outer body as its ground plane. The effectively turns the entire moving metal machine into the antenna for the transmitters. I don’t use this cliche lightly. These rooftop antennas were an absolute game-changer! We used one antenna per plant mic and they we’re photographed and established in picture! All vehicles were storm chasers, so antennas galore right? For our end of the bargain, we agreed to help the Property Department and set decoration by placing them in picture even when we didn’t need them. These antennas allowed me to use each and every plant mic to provide a flexible dailies mix as they reached up to a quarter-mile of range to my follow van when needed. Typically, we were not that far away, but wow. When we were that far away, this really made my days easier. This doesn’t mean my time capturing the plant mics in these vehicles from the follow van were drop-out free. They weren’t. As much as I feel we achieved very impressive long-distance range results, the occasional digital RF drop out would occur.
Another layer to this were the actor-worn lav mics. With the distance and physics working against them, for the most part, they would not reach all the way to me in the follow van no matter which picture car or camera car we were using. It was just too far away, the car was a metal box with faraday properties, and the transmitters were hugging the actors’ flesh. The only thing we could have done to improve this (if we had time) was to run and safety pin a mini six-foot-long dipole antenna to each the of actors’ shoulders. I have these antennas, but it also wasn’t going to be fool proof as the actors were still inside the faraday cage. So instead, I decided to use my crew’s time and energy to mount the rooftop antennas for the individual plant mics and a larger, custom-tuned one-fourth wave mobile CB radio mag mount antenna for the “Bag-Drop” rig.
CHASING MY BAG-DROP RIG
OK, the bag-drop rig. For many readers who have done plenty of car work in their careers, this will come as no surprise. But if you haven’t, please heed this advice: Creating a well-organized workflow for doing a bag-drop rig in picture cars is the most important thing you can do among all of the layers of your car- work procedure. Even with all the impressive range we achieved with the DPR-A transmitters utilizing their own rooftop antennas and allowing me to mix each plant mic from the follow van with ease, there is no way one should do this type of free-driving work without this failsafe in place. Not to mention there was no other guaranteed way of capturing the actor-worn lavs with this kind of reliability. I would never want to just “drop a bag” either. That should rarely be part of the equation. We use the bag-drop as a failsafe for post-production in the event of RF dropouts, and we also use the bag-drop as an additional layer to mix with in this twofold scenario: part one is to have the bag-drop rig equipped with an output or “hop” transmitter that I make sure has an absolutely spotless carrier frequency.
In the case of the various towns and rural areas in Oklahoma, this was in the upper B1 band around 590.000 MHz. In the event that the pod-driven vehicle got too far away from the follow van, I would subtly mix out the plant mics and mix up the feed from the bag-drop which had a more powerfully signal-boosted transmitter associated with it. Then using the aforementioned custom-tuned CB radio rooftop-mounted antenna from the bag-drop boosted transmitter, I would often get about a half-mile range! This came in handy several times and I was grateful for it. Part two of this scenario was how I would also use the bag-drop to provide me with mixable lav mic feeds from the actors. Imagine a scene where an actor is lifting himself out of the moving vehicle to do some heroic work reaching out his window up to the roof of the picture car. There is no usable plant mic near him and there is certainly no boom operator near him and the only shot at getting his dialog is by using his lav. I could just say to the director: “Don’t worry, it’s getting captured on the bag-drop!” But instead of even having that conversation, I would just mix up the bag-drop feed which I intentionally manually mixed as a heavy output of the lavs and this particular actor’s lav when I had custody of the bag-drop rig earlier before heading out to shoot the scene. I would also utilize this technique when I really needed to use an actor’s lav for a quiet line. Basically, in the absence of any auto-mix utilization, I chose to manually “mix set” the bag-drop to favor all the talent lavs so I could use those signals to my advantage in the dailies mix.
Here is a full breakdown of what was recorded as part of the bag-drop rig: ISO tracks 1-4 were redundant recordings of each plant mic that I successfully received from the follow van (but hey, redundancy is good). Then, ISO tracks 5-8 were each actor’s lavs recorded just feet away from them and likely with no RF dropouts. Timecode matched my main recorder and I had plenty of 256GB SD cards at my disposal as that recorder would often roll for hours on end, only really stopped during lunch breaks. The equipment used for the bag-drop rig was as follows: one Sound Devices 833 mixer/recorder, two Lectrosonics DSR4’s mounted inside a PSC RF 4 Pack feeding out all eight channels via AES connection, one Lectrosonics LT transmitter in B1 band to an Audio Wireless Power Booster set to 250mw feeding a DPD Productions one-fourth wave custom-tuned CB radio antenna, and finally, one Ambient Tiny ACN Lockit box keeping it all in sync. The entire bag was powered by a PSC PeliLiFe battery feeding every device except the Audio Wireless signal booster. For this, I had an isolated power source with a half-sized eSmart battery both housed together in a bespoke 3D-printed holster by Coga Sound.
CHASING THE WEATHER
The downside in shooting this film in the summer in Oklahoma was the real possibility of seeing (and then getting shut down by) incoming severe weather. Our Camera Operator once said to me one of the more frustrating things about doing this movie was right when the sky started to get beautiful with ominous weather, it was time to shut down for what was typically a lighting delay. The studio mandates a protocol where any severe weather that includes a lightning strike within eight miles of the work area requires the work to stop, and crew must take shelter immediately for a half-hour. Every new lighting strike resets the clock. This would often lead to us waiting around for hours after not completing the scene at hand. And oftentimes after a few hours, we would have to wrap as the storm would linger on past when our day would have completed. This made things complicated and sometimes it would take us longer to complete certain sequences than originally planned. When I would take shelter either in a store front or our own cube truck, I would often have a stereo mic already planted outside and I would record hours of thunder sounds while we waited.
The waiting was made easier by the good conversation with our colleagues. People were always eager to get back to work, but also grateful for the safety protocol and the opportunity to take a beat and get to know their fellow crew members without the hustle of the day-to-day work. Between the challenges of the weather and the anticipated WGA and SAG-AFTRA labor strikes, we were racing to the finish line.
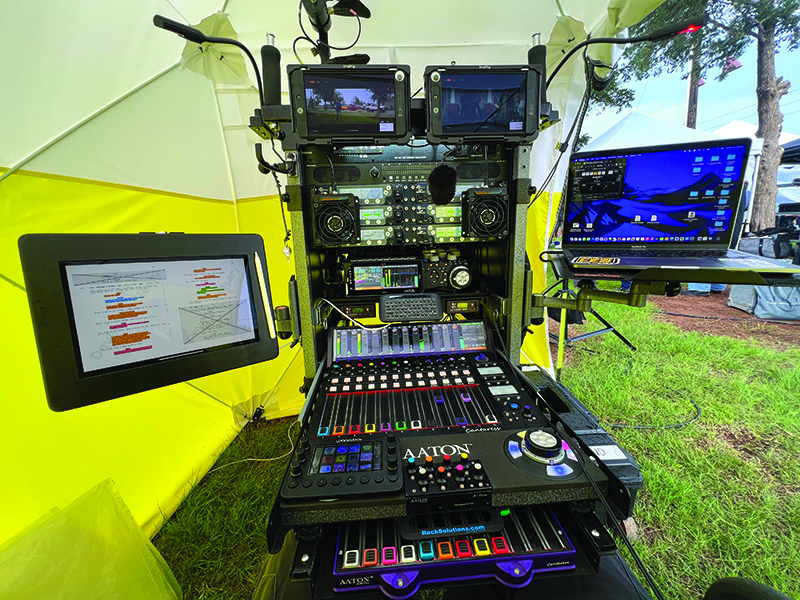
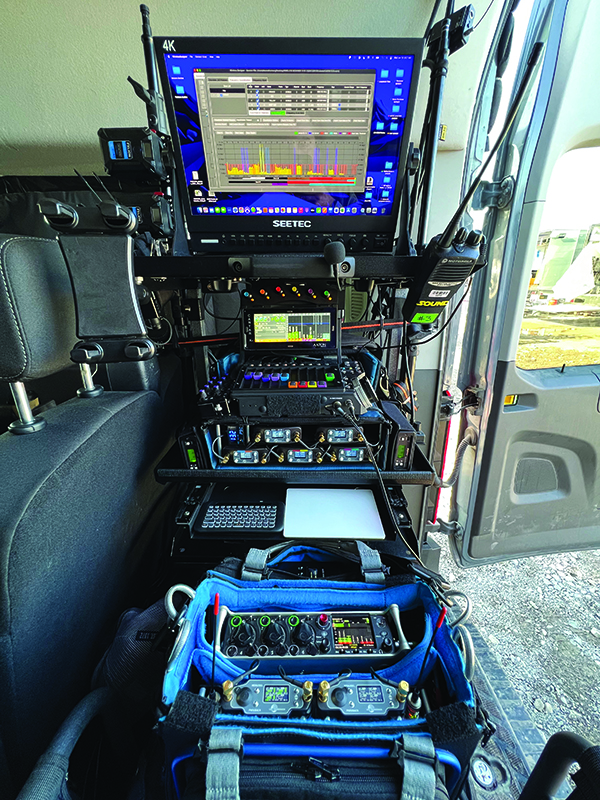
CHASING COMPLETION
As I write the majority of this article during the months of the SAG-AFTRA strike, it bears some explanation that we had to shut down filming with just under a month left until completion of principal photography. My intention was to write half of this section on this side of the finish line, and the second half once we made it over the line! We have such wonderful cast and crew who have worked so hard to bring this movie to fruition. During this strike time, I have been watching dailies every day and getting really nostalgic. I also had some additional equipment modifications done and bespoke accessories made with the express intention on using them on the shoot when we can finally reboot the production. I’m so excited to use the newly developed tools and am happy to be continuously learning from every shoot that I embark on. But most importantly, I can’t wait to get back out to Oklahoma and see everyone’s faces again and bring this very special production to a successful completion. Wish us luck!
OK, Future Devendra here. Now I can open up my laptop to finish this article as I just got back to LA after a whirlwind of a three-week shoot back out in Oklahoma! This time, we filmed in Spencer, Oklahoma, to finish up our rodeo and motel work, Chickasha, Oklahoma, to finish up some major storm aftermath in a neighborhood we took over out on Drummond Ranch in Pawhuska, Oklahoma, to finish up some very scenic work for some pivotal scenes, and then of course, we competed several days on stage at Prairie Surf Studios in Oklahoma City, Oklahoma. This leg of production was an absolute dream! Pretty much everyone came back to finish, which I believe is a testament to their love of the project and big affection for our director Isaac and the production team. An admirable detail I noticed as we powered through the remaining work is that pretty much every department must have also done some sort of bespoke tweaking to their kits that had inadvertently or deliberately made their jobs more efficient and customized to the movie. This made me feel so at home to work with a crew at this level and with a little bit of vindication instead of feeling “nerdy” for doing the same with my kit. The three weeks went by so fast and as I write this around the holidays, I’m not quite settled in, and I haven’t left “work mode” yet. I’m really missing Oklahoma and the team of absolute stellar professionals all around. Our wrap gift from our department were Twisters sound jackets and they were a hit! Thankfully, we handed them out in the winter instead of summer! I hope everyone enjoys the movie as much as we enjoyed making it! Come see it on the big screen and “if you feel it, chase it!!!”
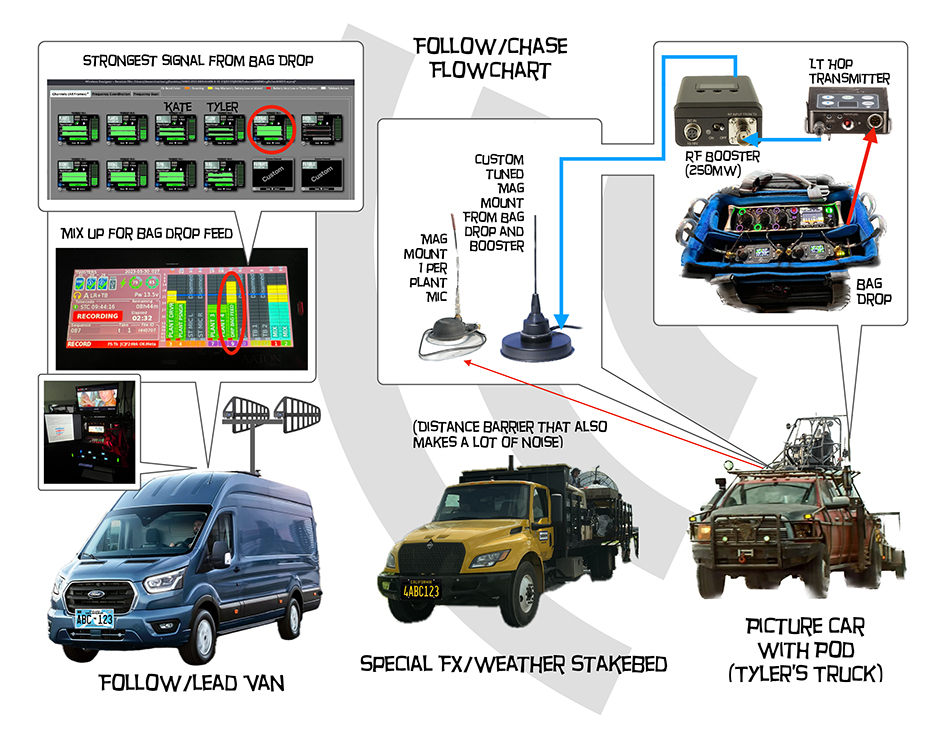